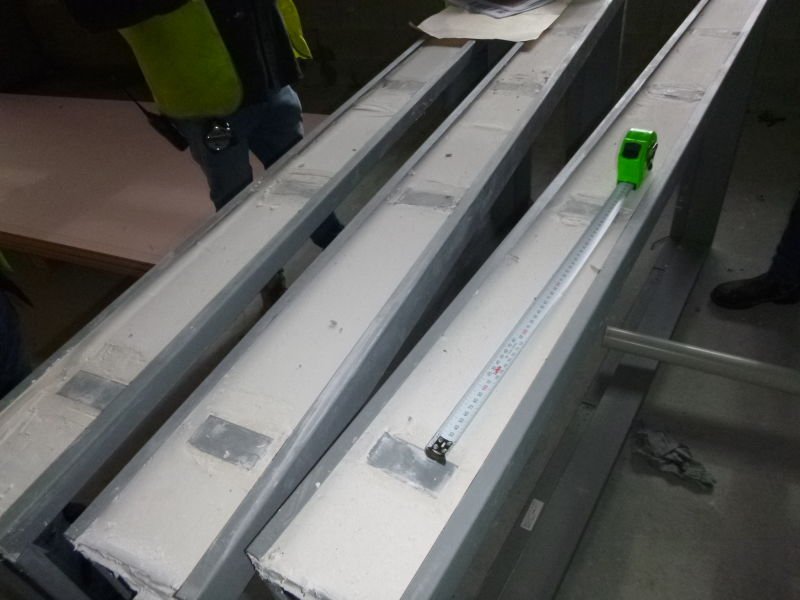
asdf
asdfsdf
Metal fire door frames are a tested system so it’s critical each frame is manufactured to meet the requirements of the fire test to remain compliant.
Relevant Standard / AS 1905.1-2015
Components for the protection of openings in fire-resistant walls
Part 1: Fire-resistant doorsets
There are several key elements that need to be monitored in respect to the manufacture and install in accordance with each manufacturer’s test reports / construction manual.
Test report | It is important to have the test report for the system. Request it when letting the contract | |
Metal thickness | Refer test report – usually 1.1mm min thickness but may be greater | |
Door stop | Min 25mm as per the standard | |
Fixing points / straps | Typically 300mm maximum between fixings Monitor closely as it has become an issue with manufacturers increasing spacings creating a likely non-confirming product. Refer photos below |
asdfsdf
Insulation | Grout filled, prefilled insulation or site plasterboard backed dependant on what the frame is being fixed to and strictly as per the tested system details (no expander foam or the like) |
Frame install | Frames installed square/plumb/not twisted |
Clearances | Doors installed with max 3mm gaps to the jambs and head Doors installed with max 20mm under door to floor substrate and 10mm floor covering across full width of the door |
Metal hardware fixing plates (in fire doors) | Doors have metal plates to locate the door furniture Check the door has a small hole drilled in the top on the hinge side. If the hole is there, then the door is installed the right way up. If there is no hole in this location, then the door is likely installed upside down or back to front. Reinstall the door correctly or replace as required |
Screws | All screws in hinges MUST be compatible metals, e.g. NO zinc screws in stainless steel hinges. Refer image below |
Tag | Door frames and doors to have correct labels as per AS 1905.1 clause 6.1.4 (must include year of manufacture). Refer image below |
In addition to the key elements, consider sensible door/door frame quality, including:
External doors frames requiring weather protection (hoods or the like) |
Door frames preferably should not be ‘buried’ in wet area bedding or concrete (where this occurs the frame must be suitably prepared with metal primer and waterproofed) |
Use stainless, epoxy painted or galvanised frames in corrosive environments. Use stainless within 100m of salt water |
Utilise bat wing seals to provide a seal between airconditioned and humid external air in corrosive environments. This reduces saltwater forming on the frame |
Jambs and head MUST be back filled in accordance with manufacturer’s details |
All doors MUST be painted top and bottom |
Ensure owner’s manuals have clear instructions on cleaning the doors/frames to avoid corrosion |
Ensure owner’s manuals have information on the tested system door clearances (to avoid maintenance companies defecting doors against incorrect information post completion) |
Please contact the Quality Team if you have any questions
Phone 1300 HUTCHIES